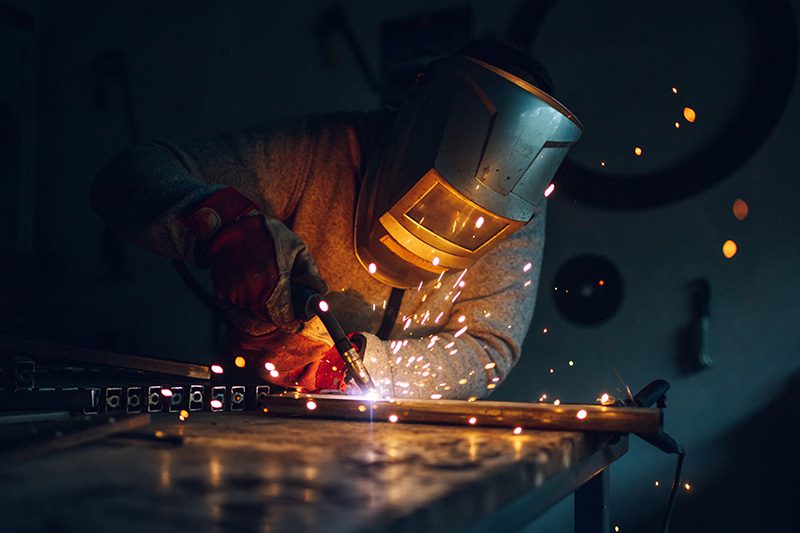
Joining Dissimilar Materials: Major Considerations and Difficult Lessons Learned
November 17, 2020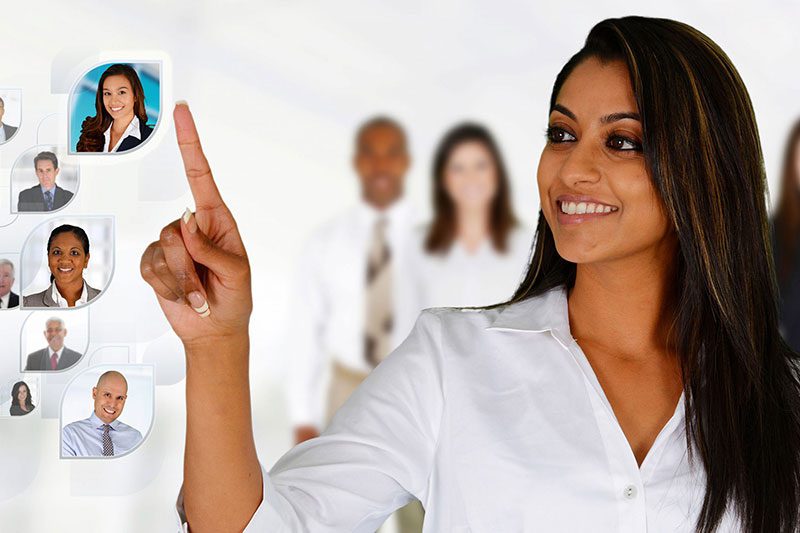
Navigating Engineering Staffing and Services in the Post Pandemic World
April 22, 2021Analysts expect that the need for an increasingly efficient product development cycle will cause demand for Finite Element Analysis (FEA) to grow by over 9% in the next five years. Are you using Finite Element Analysis in your design process yet? The cost savings benefits of FEA could be the difference between a successful project and one that is riddled with added costs and reduced performance.
FEA can help you cut costs and design higher-performing products.
Find out more about what FEA can do for your business. You’ll be ready to add this powerful tool to your design cycle.
The Basics of Finite Element Analysis
Finite Element Analysis is a way to model the stresses on an engineering design mathematically. It’s a digital platform that engineers use to test designs against predictable forces and physical effects like vibration, heat, and tensile or compressive loading.
FEA lets you see how a design will hold up in real-world situations. If the design fails, you can see where the fault occurred and how it might propagate.
You can apply FEA to any physics problem that you can model mathematically.
Finite Element Analysis works by breaking an object down into many small elements. This mathematical technique is called the Finite Element Method (FEM).
Once you have a digital mesh of the design made up of small elements, mathematical equations predict each element’s behavior. The equations you would typically need to calculate the effects of the forces acting on a design are often partial differential equations. FEM lets you break the large-scale equation set down into simpler algebraic equations.
The smaller equations combine to predict the behavior of the whole model. As long as the model is broken down into enough elements, the prediction will accurately represent reality.
Types of FEA
Several types of Finite Element Analysis are available. The kind you use depends on the physical behaviors and interactions you want to simulate.
Linear or Non-Linear
Linear FEA assumes that the stiffness matrix, such as material properties and geometrical configuration, doesn’t change significantly during the analysis. It helps you simulate cases where you don’t expect the structure and conditions of the analysis to change in response to the applied load.
Non-linear can handle more complex situations. Non-linear FEA is useful in cases where material properties change with force, as in plasticity. Non-linear FEA also helps you model dynamic time-dependent problems like vibration.
Static or Dynamic
Static analysis works for situations where the load is constant. The system doesn’t change over time.
Dynamic analysis is necessary if the system itself, the load application, or both might change over time. Dynamic analysis also takes acceleration and inertia into account.
Comparative or Absolute
FEA can usually give you absolute results with a high degree of accuracy. However, most companies are often more concerned with comparative results. Comparative analysis can show you whether design changes will cause a part’s performance to improve or degrade.
Cutting Costs with FEA
One of the main benefits of using Finite Element Analysis is that you can cut costs without sacrificing quality. FEA has several advantages over physical testing in terms of cost.
1. Fewer Physical Prototypes
Using FEA means you don’t need multiple versions of early prototypes. You save money on materials and labor. Developments in 3D printing have made producing prototypes easier, but the costs are still higher than FEA.
Avoiding the trial-and-error approach reduces your use of materials. You don’t end up with wasted materials from failed parts.
2. Capitalize on Efficient CAD Modeling
CAD modeling can be fast and efficient. In the traditional product cycle, the cost peaks at the end of the manufacturing phase. Moving the majority of the design and analysis to the 3D CAD phase reduces those costs.
3. Optimize Design through Iterations
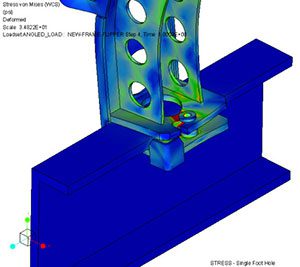
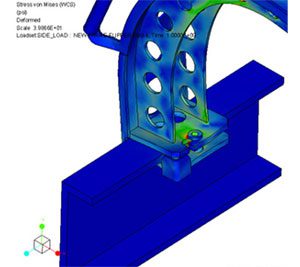
FEA helps you maximize the efficiency of your product design. You can analyze design changes to ensure you meet safety and performance standards while reducing material consumption.
In addition, FEA pinpoints the causes of design failures. Through FEA, you know precisely which design features you need to modify. You don’t unnecessarily reinforce features that weren’t a contributing cause for a failure.
Iterative mathematical solutions through FEA can promote a stable, rigid design that minimizes fabrication costs, material usage, and product weight.
4. Avoid Sudden Cost Increases in Later Phases of the Manufacturing Cycle
One key cost saving benefits of FEA is finding and fixing any problems in the product design with FEA during the early stages of the design-to-manufacture cycle saves money. Tooling and CNC machining are expensive. Changing a part multiple times can rapidly increase your costs.
FEA lets you verify the product before committing to a manufacturing setup. You don’t waste time and money setting up tooling and manufacturing processes for a product design that doesn’t work out.
5. Faster Turnaround Time
FEA gives you a faster design cycle. You aren’t tied to machine shops and manufacturing schedules for prototypes. You can test a new design using FEA within hours instead of waiting days or weeks to test a physical version.
You can test many design versions quickly and accurately. You can move forward with a successful design faster than if you needed to test multiple designs using physical prototypes.
Other Advantages of FEA
Finite Element Analysis gives you advantages even beyond cutting costs. It can help you design a safer, better-performing product. It can also help you present your work more effectively to non-engineers.
Model the Interior and Exterior of the Design
FEA models the internal force response as well as the external reactions of the design. You can see how forces will affect the entire structure. This lets the designer see where and why failures may occur.
Insight into Local Effects on Small Areas of the Design
FEA gives you insight into how stresses within one piece of the product affect materials in another piece. You can see what local effects will do to a small area of the design.
Safe Simulation of Potentially Dangerous Failure Conditions
FEA lets you simulate potentially dangerous conditions. Testing some types of load conditions may not be practical and could be dangerous. Some types of product failures could also be hazardous.
You can still see how your product would react in those conditions using FEA.
Present Designs to Non-Engineering Stakeholders
FEA is a visual tool. When you need to prove the performance capabilities and integrity of a product design to non-engineers, FEA gives you evidence that often makes a non-expert feel comfortable.
Stakeholders like corporate executives, investors, and marketing personnel often want more than a physical model. Research suggests that presentations with a visual component are 43% more persuasive for the audience. FEA gives you another way to present your design convincingly. Another persuasive argument is the cost saving benefits of FEA; we have never met an executive who wasn’t interested in reducing a budget effectively.
Adding Finite Element Analysis to Your Design Process
When you’re ready to cut costs and improve your design process, Finite Element Analysis is the tool you’re looking for. You can trust ENSER with your FEA needs.
Why pay thousands of dollars for a software license and then spend the time and money to train your employees to use it? Rely on our decades of experience and investment in the latest technology. We’ll give you the quality solutions you need.
Founded in 1947 in Philadelphia, Pa, ENSER started with humble beginnings. First opened as a tool design company, our company has grown to three divisions: Engineering, Manufacturing, and Staffing.
With over 70 years of experience in the industry, our project management and engineering solutions pave the way.
Our history defines us. We can take the right steps to define yours.
Engineering Services
Whether you need engineering services for the world’s largest power rollers or something smaller, ENSER Corp, has the engineering skills and know-how to complete your project.