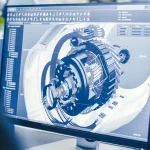
Maximizing Efficiency and Protecting Your IP with Turnkey Manufacturing Solutions
January 27, 2025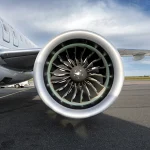
Optimizing Aerospace Manufacturing with ENSER’s Turnkey Manufacturing Solutions
March 4, 2025The debate over the large-scale implementation of wind turbine farms as a clean energy solution continues to evolve. Proponents highlight technological advancements, operational efficiency, and environmental benefits, while critics focus on reliability, material limitations, and infrastructure costs. What remains undisputed is that wind energy is an abundant, renewable resource that produces zero direct emissions, positioning it as a viable alternative to fossil fuels. However, to fully integrate wind turbines into power generation on a national scale, engineers must address key technical, economic, and logistical challenges.
The Economic and Environmental Trade-Offs
The financial feasibility of wind energy remains a complex equation. While wind itself is free, the costs associated with turbine manufacturing, installation, maintenance, and grid integration create significant obstacles. Transmission infrastructure must be adapted to accommodate geographically dispersed wind farms, and offshore installations—while offering stronger, more consistent wind conditions—demand higher capital investment due to transportation and maintenance difficulties in harsh marine environments. On a smaller scale, landowners benefit economically by leasing their property for wind farm installations, offering a localized incentive for renewable energy expansion. However, critics argue that subsidies and tax incentives distort the true cost-efficiency of wind power compared to traditional fossil fuel sources.
Material Innovations and Structural Durability
Engineering advancements in composite materials and gearbox efficiency are continuously shaping the future of wind turbine technology. Turbine blades, traditionally constructed from fiberglass and carbon fiber, are under scrutiny for their durability and environmental impact. Reports of offshore turbine blade failures, with fragments washing ashore, raise concerns about long-term sustainability and material disposal. Additionally, large-scale offshore turbines face significant mechanical stresses due to high wind shear forces, necessitating rigorous materials engineering and predictive maintenance strategies. The industry is also addressing ecologists’ concerns over structural vibrations potentially affecting marine life, adding another dimension to offshore wind development challenges.
Engineering Solutions to Reduce Failure Rates
As wind turbines increase in size –comparable in height to the Status of Liberty—understanding the mechanical stressors on these structures is crucial. Advanced finite element analysis (FEA) and real-time structural health monitoring are being leveraged to predict failures and optimize component life expectancy. Lubrication requirements for turbine gearboxes continue to drive innovation in low-friction coatings and predictive maintenance technologies that reduce downtime and enhance overall efficiency.
The Reality of Wind Power’s Carbon Footprint
While wind power is often promoted as a zero-emission energy source, critics point out the substantial carbon footprint associated with manufacturing, transportation, and installation. The construction of each turbine involves vast amounts of concrete and steel, often transported using fossil-fuel-powered equipment. Additionally, the ongoing need for lubrication and grid infrastructure adjustments factors into the overall sustainability equation. Despite these challenges, ongoing technological advancements are improving the efficiency, longevity, and recyclability of wind turbine components, positioning wind energy as a continuously evolving solution in the global transition to renewable power.
Frequently Asked Questions About Wind Turbines in Power Generation
How ENSER Corporation Supports the Wind Turbine Manufacturing Industry
As the global demand for renewable energy grows, ENSER Corporation, based in Cinnaminson, NJ, is uniquely positioned to support the wind turbine manufacturing industry. With over 78 years of experience in engineering and manufacturing solutions, ENSER provides critical services that enhance the efficiency, reliability, and scalability of wind turbine production.
- Precision Tooling and Fixture Design for Wind Turbines
ENSER specializes in designing and fabricating custom tooling and fixtures that can be tailored to the needs of wind turbine manufacturers. Our solutions improve assembly accuracy, streamline production processes, and reduce downtime, ensuring that your operations meet high-volume demands with precision.
- Advanced Mechanical and Structural Engineering
Wind turbines demand robust and lightweight designs to optimize performance and withstand harsh environmental conditions. ENSER’s engineering team offers expertise in designing critical components such as towers and gearboxes, ensuring they meet industry standards for durability and efficiency. Our structural engineering experience as applied to wind energy guarantees high performance and reliability.
- Finite Element Analysis (FEA) for Wind Turbine Components
Using innovative simulation tools, ENSER conducts detailed stress, fatigue, and thermal analyses on complex systems like wind turbines and their subcomponents. These insights help manufacturers improve reliability, extend component lifespans, and optimize material usage, reducing costs without sacrificing performance.
- Custom Manufacturing Support and Automation Solutions
ENSER provides automation systems and robotic integration services tailored to wind turbine component production. From blade fabrication to tower assembly, our manufacturing support solutions boost efficiency, enhance quality control, and reduce waste.
- Heavy Equipment and Lift Assist Devices
The large-scale components of wind turbines require specialized lifting and handling equipment. ENSER designs and fabricates custom lift-assist devices and material handling systems that prioritize safety and ergonomics while ensuring seamless assembly and transport of large and awkward parts.
- Prototyping and Product Development
ENSER can support wind turbine manufacturers with rapid prototyping services to refine designs before mass production. This process minimizes risks, reduces design flaws, and ensures components are optimized for manufacturability and performance.
- Maintenance, Repair, and Overhaul (MRO) Engineering
To extend the operational lifespan of wind turbines, ENSER can provide engineering services focused on maintenance and repair. Our team can design tools, fixtures, and processes that streamline turbine maintenance, reduce downtime, and optimize overall system performance.
- In-House Engineering and Contract Staffing
Technical marketplace engineering talent is more transient than in previous generations. Remote or hybrid employment is part of the current climate that project managers must work with, through or around. While ENSER has a fully qualified engineering team in house to complete tasks offloaded from manufacturers’ own departments, there are opportunities to bolster an engineering department with short term talent that is single- or multi-project related. ENSER’s staffing division can provide fully vetted engineering talent for placement into an undermanned engineering department. These placements can be strictly attached to a singular project or be attached to the department for extended periods of high-demand activity.
Ready to enhance your wind turbine manufacturing process?
With decades of experience across various industries, ENSER Corporation combines engineering expertise, manufacturing expertise, and a commitment to innovation to support all styles of power generation equipment, including the wind turbine manufacturing sector. Whether you need advanced tooling, structural analysis, or custom automation systems, ENSER delivers solutions that meet the unique challenges of traditional and renewable energy production.
Let us help you power the future.