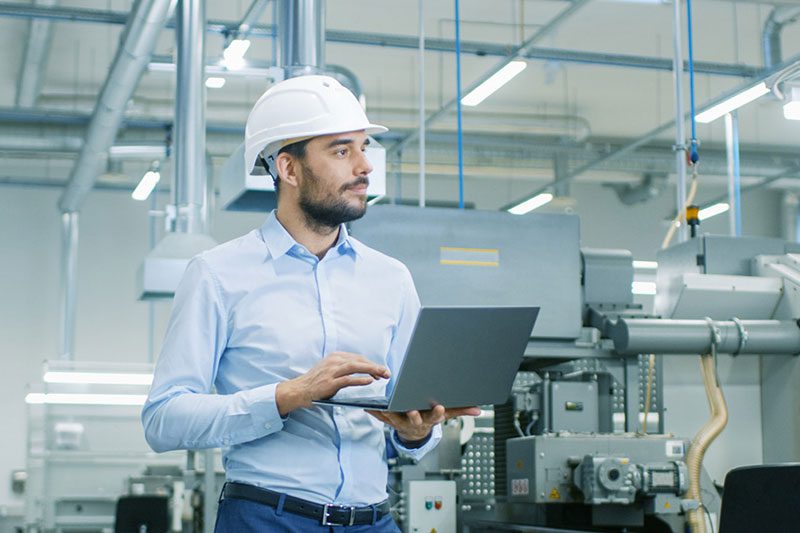
7 Strong Benefits to Outsourcing Engineering Work
October 12, 2020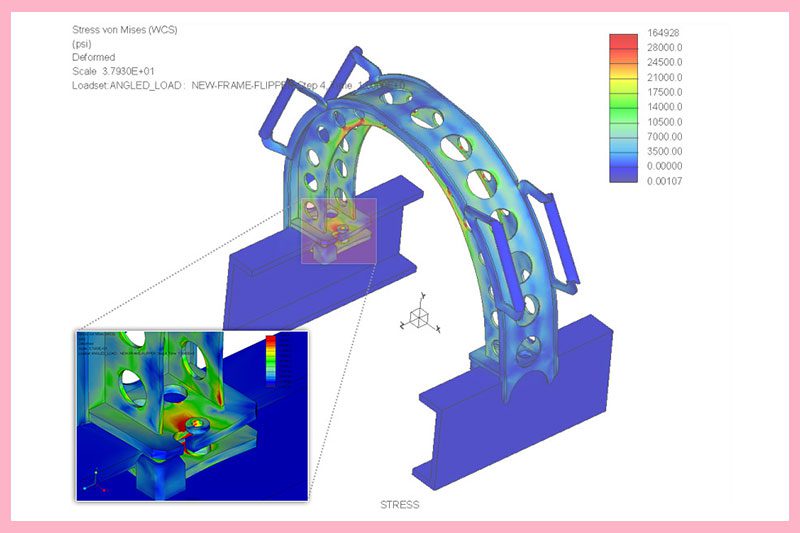
Cost Saving Benefits of FEA – How Using FEA Can Reduce Costs and Increase Performance
March 9, 2021If your business manages engineering projects, manufacturing, research, or development departments, you’ll probably already be aware that joining dissimilar materials is increasingly common. We’re talking about materials such as polymers being joined to metal using heating and bonding methods. Polymers are often chosen because they’re robust, light, low cost, and have elasticity. In contrast, metals are more likely to be used where strength and stiffness are a priority. But, a combination of polymers and metals can provide more significant product and design flexibility. This reason is why there’s such high demand for parts with metal-to-polymer joints. This fact is especially true within the aerospace and automotive industries. But, joining dissimilar materials commonly involves welding dissimilar steels together. If you’re not experienced with this process, you might learn some significant lessons the hard way. We know we had to! So what are the preliminary engineering design considerations when welding dissimilar materials? Read on to find out!
Considerations
Welding dissimilar steels isn’t a simple process. There are several considerations to take into account if you want your weldments to perform adequately:
Knowledge
When you’re welding two dissimilar steels together, you need to know whether the filler metal is compatible with the metals you’re welding. Without this information, the part may not be strong enough or crack. It’s essential to know the chemistry of the base metals involved. You can get this insight via a coupon analysis, spark test, or a look at the original blueprints.
Design Requirements
What will be the use of the finished design? Will it experience high temperatures or stresses after the welding process? If so, you need to factor this into its design. Otherwise, the finished weldment may not serve its intended purpose. Ensure the joint design and the two dissimilar materials’ thickness is sufficient for whatever its intended use is.
Preheat and Heat
Different steels may require different preheat temperatures. So, knowing each metal’s characteristics and behaviors are essential in the pre-welding and design process. Also, it’s imperative to consider the heating and cooling rates of the dissimilar steels. These affect the joint’s microstructure, affecting the strength and precision control of the heat input. Once base materials are preheated and welded, they cool, and as they do so, they may contract by different amounts. So, the fused metals may experience high stresses that cause cracking or distortion. You should evaluate each material that needs heating. Generally speaking, when you’re welding dissimilar materials with different preheat considerations, you opt for the higher temperature.
Corrosion
When joining dissimilar metals, it’s essential to consider galvanic corrosion. When two dissimilar metals are joined and then placed in a wet environment, it completes an electrical circuit. Some metals give up their electrons more quickly than other metals. Consequently, they corrode faster.
Difficult Lesson Learned
We’ve already alluded to the fact that welding dissimilar steels can be difficult. Recently, ENSER was approached by one of our clients to design and build a 260 ton turn down fixture. We were working with a crane with weight limitations where they performed the lifting. These restrictions are why we designed the fixture to use some high alloy – strong metals with a high strength to weight property. The materials we used were A-572 steel, A-514 steel, and 4140 steel. To ensure these components’ manufacture was sound, ENSER called for the welding performed to meet the AWS D.1 standards. However, our Quality Assurance team’s closer examination of the fixture before delivery revealed that this welding standard had not been achieved. We immediately requested a thorough investigation of the welding. Through this, we discovered that one of ENSER’s vendors did not have the correct process or WPS in place to weld A-514 or 4140 steel. ENSER found out that there were pervasive issues with the welding of some of the various alloy materials. With this harsh lesson learned close to delivery, ENSER committed to researching the 4140 material more closely.
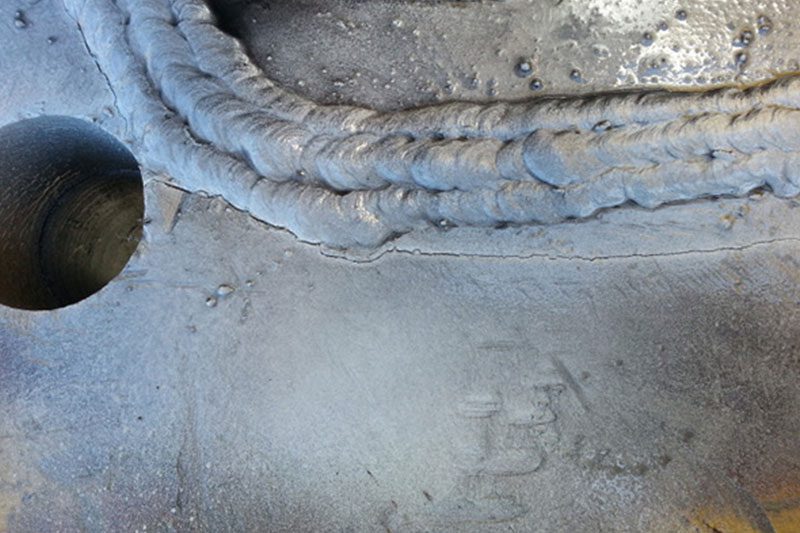
Other Things Worth Noting
We had to know how it would perform when welded. As a result of our research, we re-engineered the attachment of the 4140 material to the main beam and the side beams, which would remove any possible issues caused by the welding. In other words, we secured the 4140 steel in a way that removed the need for welding on this material entirely. We replaced the material and completed the repair.
So, what did we learn?
This recent project served as a reminder that research is a crucial step in welding dissimilar materials. Before you design a welding project, make sure you understand how different materials react and whether they are compatible. It’s also vital to make sure all vendors have the necessary training and experience to fabricate with proper WPS to ensure the work is up to AWS standards.
Looking for Engineering and Manufacturing Solutions?
ENSER’s 70+ years of industry experience ensures we stay on top of all the best practices for welding dissimilar materials. We have learned the difficult lessons and emerged with improved knowledge and research so that you can trust our standards will excel in the industry. Our team of professionals will support your engineering and manufacturing requirements and provide you with end to end solutions that other engineering companies cannot offer. Our extensive expertise puts us in an ideal position to solve any design and manufacturing issues you may have. Contact us today for a same-day response.