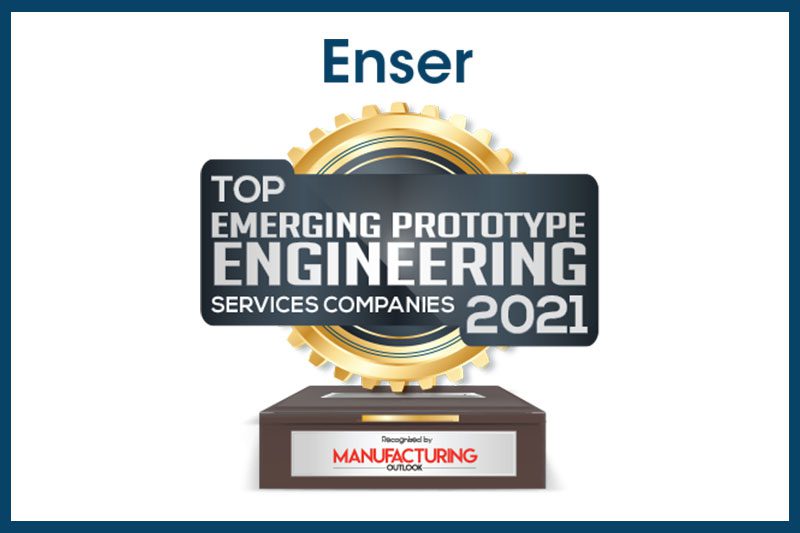
ENSER is Ranked a Top Emerging Prototype Engineering Services Company in 2021
September 21, 2021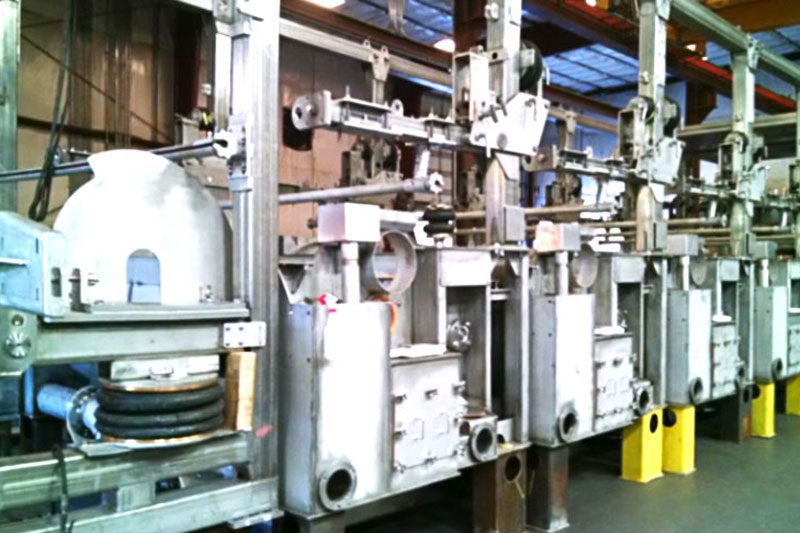
Advancements in Vat Forming Technology in Paperboard Manufacturing
March 22, 2022Did you know that up to 80% of a product’s manufacturing costs depend on the details of the design decisions you make? So if you want to minimize costs and maximize efficiency, taking time to design the product efficiently from the start can reduce problems at the end.
This is where design-for-manufacturing, or DFM, comes in. DFM can help you make the best choices for the product and your business.
Learn more about how DFM can help lower costs.
What Is Design-For-Manufacturing?
DFM is the process of designing products for ease of manufacturing, which often leads to reduced costs and saved time. The product has to use parts that are easy to mass-produce and assemble to achieve this goal.
Unlike functional engineering, which focuses solely on the performance of a product, DFM also focuses on saving on production costs. By using design principles and improvements and ensuring that some key strategies are in place (like creating parts that can be made with standard tools instead of custom ones), DFM can help you create something affordable to mass-produce.
For design-for-manufacturing to offer the benefits that you want, you must implement it at the right time. The best time to bring DFM to the table is at the beginning of the design process after the initial concept development is complete. Although it is possible to incorporate DFM practices during any part of the design process, the further along you are, the more likely you’ll end up needing to redesign aspects of your product.
How DFM Helps Reduce Costs
DFM can help reduce the costs of manufacturing a product in several ways. Let’s take a look at how it can benefit your business.
Reduces Operations
DFM works by eliminating unnecessary steps. The more operations you have to perform before you finish the product, the higher your costs will climb. Not only does this save you money, but it also helps avoid errors since the more steps that are needed will increase the chance of mistakes.
DFM works by seeking alternatives to reduce complexity and make the product more straightforward and faster to create. As a result, it can reduce labor costs significantly, as referenced by the 47% average cost savings illustrated in this MIT research paper.
It also reduces secondary operations. With DFM, you will choose the processes that can offer efficiency. One example of the design for manufacturing examples that can illustrate this point is that laser welding is much faster than TIG or MIG welding while also not requiring finishing operations. Therefore, it can be a better, cost-saving choice.
DFM can also reduce the entire product development cycle and assembly time significantly, as referenced by the 45% and 64% respectively from these examples.
Improves Material and Process Tolerance
Tolerancing refers to the variations that can occur in the product before the design and function no longer work. Tight tolerances make inspections take longer and will end up costing you more. DFM can help improve material and process tolerance.
An engineering design for manufacturing example of this can be how material comes out of a mold in an injection molding process. If the mold is not tapered enough or does not have drafts to release the material from the tool, then the final product will not match the design drawings.
DFM helps you optimize the tolerances so that you can create a product that will not need such tight ones to still function. It will also analyze how tolerances will work in your assembly and find ways to improve the process.
With DFM techniques, you will focus on understanding how the manufacturing equipment works, as well as the limitations each tool has. By working around standard machine tolerances, the part can work on any similar machine.
Standardizes Parts
One of the main benefits of using Finite Element Analysis is that you can cut costs without sacrificing quality. FEA has several advantages over physical testing in terms of cost.
One of the most effective ways that DFM can save on costs is by identifying similar parts and creating a standardized option. This similarity can be achieved by using the same design, materials, or COTS (commercial off-the-shelf) items. As a result, you will see significant reductions in part counts. For example, Whirlpool achieved a 29% reduction in part counts this way.
Standardization reduces the inventory and scale-up requirements. With DFM, you will be able to create parts that you can use across product lines and parts you can reuse within the overall design of a product.
Consider the part’s contours. DFM helps you create a simpler part that can be made on a three-axis machine and not a five-axis one.
DFM can also encourage you to make modular designs, which helps when modifying the product. By using standard components and not custom-made options, you can expect to see a significant cost reduction.
This standardization includes tools. You do not want to design parts that require special tools in the manufacturing process. With DFM, you too can see a 64% reduction of necessary assembly tools.
Reduces Setup Time
You can reduce setup time with DFM by reducing the number of operations or making assembly steps simpler.
One of the most important design for manufacturing and assembly examples to consider for reducing setup time is printing 3D work holdings. This can aid your workers with issues like alignment, assembly, and inspection processes.
Simplifies Design
The simpler your design is, the less time it will take to assemble and the fewer costs it will create. Therefore, DFM suggests that you make multi-functional parts and try to make the product’s assembly as simple as possible.
One way of doing this is to avoid creating left-hand/right-hand parts. Designing parts that are each other’s mirror images will slow down production. Instead, use paired parts, which can work on either side of the product.
DFM also focuses on creating symmetrical parts. Parts that are almost symmetrical can create problems on the production line since workers can easily mistake one part for another. That means wasted manufacturing time.
If you cannot go for perfect symmetry, choose to go entirely asymmetrical to avoid confusion.
It is also important to use securing methods that are quick, like snap fits. You do not want to go for options that require bolts or glue. With DMF, you can reduce the assembly time to separate fasteners by 50%. You may also want to consider design-in alignment.
Implement Design for Manufacturing
Your business will only improve if you choose to implement design-for-manufacturing techniques. As a result, you will save on costs while not compromising product quality.
Contact us today to learn how we can help your business!
Founded in 1947 in Philadelphia, Pa, ENSER started with humble beginnings. First opened as a tool design company, our company has grown to three divisions: Engineering, Manufacturing, and Staffing.
With over 70 years of experience in the industry, our project management and engineering solutions pave the way.
Our history defines us. We can take the right steps to define yours.
Engineering Services
Whether you need engineering services for the world’s largest power rollers or something smaller, ENSER Corp, has the engineering skills and know-how to complete your project.